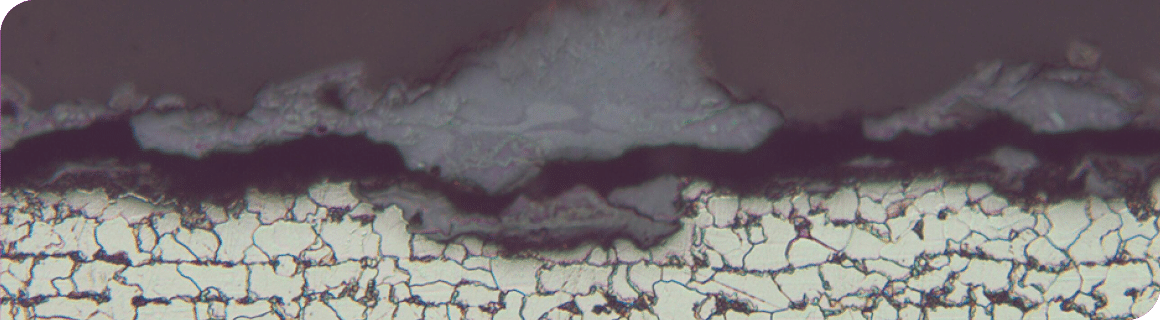
Range of Services
Long-term, continuous support for operational optimisation (online and offline)
Corrosion and erosion often affect pressure-bearing materials and their metallic or ceramic protective layers for short periods of time and locally with extremely different dynamics (rates of wear). This can lead to unexpected and sudden pipe leakage which in turn results in unplanned downtime and usually high repair costs.
01 Measures accompanying inspections
– boiler inspection in un-cleaned and cleaned conditions allow a timely prevention of damages.
Anticipatory maintenance can prevent unplanned shutdowns, provided it includes expert inspections.
We undertake such measures in both un-cleaned and cleaned condition of the boiler. In doing so, we examine all the accessible components of the entire flue gas path. We record the spatial and temporal dynamics of corrosion and erosion and ultimately gain a detailed, meaningful picture of its condition. In our experience, a step-wise supervision leads to the best possible result.
Step 1: Inspection in un-cleaned condition
Step 2: Inspection in cleaned condition
Step 3: Quality-accompanying measures in the inspection process
In un-cleaned condition, local anomalies in the properties of the fouling (including shape, thickness, colour, hardness, melt flow) provide us with important indications of the special conditions that are occurring there. From this we can deduce potential corrosion and erosion risk areas in the boiler.
In cleaned condition, we look at all relevant heat exchanger surfaces and pay special attention to the previously identified risk areas. This assessment is seen through the eyes of our experienced specialists and is supported by illuminating the heat exchanger surfaces with ‘grazing light’, shone from a flat angle. This enables us to identify the areas most affected by corrosion and erosion in the accessible areas — from spot checks to 100 per cent of a component. We mark these areas and then evaluate them by measuring the residual wall or protective coating thicknesses.
We offer quality-accompanying measures that run in parallel to the supplier’s repairs and application. Here we provide a neutral, additional impulse during the application of materials to ensure that quality requirements are reliably met. The essential aspect of this is that we can derive the specific quality requirements from the assessment of the subsequent operational load profiles, allowing to support the achievement of customised performance characteristics of the materials.
A corresponding CheMin database helps to archive and document all the data that is generated. Over the course of several revisions this makes the component’s development and its remaining useful life-time clearly recognisable for the operator and maintenance measures can therefore be timed perfectly.
This procedure can be applied to pressure-bearing materials and the protective coatings that are applied to them (for example cladding or thermal spray coatings).
Our experience clearly shows that initial optical observations followed by the marking of particularly conspicuous areas based on them are clearly superior to grid measurements of the residual wall or protective layer thicknesses. Grid measurements do not detect local anomalies. For example, a grid measurement at the crown of the pipe would fail to detect possible erosion on the pipe flank, supposedly leading to an incorrect assessment of the condition of the pipe.
02 Measures accompanying operation
– Tests, findings and sensory data reveal process characteristics that make it possible to optimise the suitability of materials and the performance of the entire plant.
The more complex and variable the chemical side effects of the fuels are, the higher the demands on the properties and quality of the materials used and their application. This is especially true for the “difficult fuels” waste, RDF, biomass and sewage sludge, but it also applies for fossil fuels and co-incineration.
It is often the case that the individual trades involved in the construction of such incineration plants are unable to adequately assess the subsequent utilisation requirements. Particularly aggressive fuel, the high energy efficiency of the plant, long travel times or the need for high availability can trigger extreme demands that are difficult to estimate.
Our in-service measures use the real process to:
- investigate material properties
- support material development
- detect process characteristics and causes of corrosion and fouling
- determine and optimise process properties
- detect and evaluate the effects of specific changes (tests)
We are happy to cooperate on a confidential basis with the manufacturers, processors and users of the materials. We make our findings and indications available for the further development of materials (not only power plant materials) and their manufacturing processes.
As a development partner for the improvement of materials and applications, we prefer to rely on practical testing. This means that we develop specified material probes depending on the problem and the task at hand, which we then use under real and targeted conditions (CheMin probes and sensors). This allows us to demonstrate the performance characteristics of materials much more clearly than would be possible through laboratory tests. Our experience shows that this procedure is often superior to the use of standardised tests and corresponding test rigs.