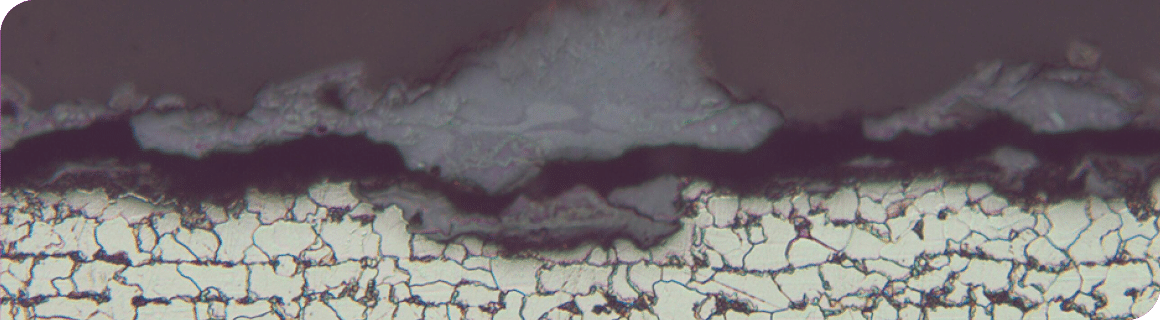
Leistungsangebot
Langfristige, kontinuierliche Unterstützung bei der betrieblichen Optimierung (online / offline)
Korrosion und Erosion wirken auf drucktragende Werkstoffe und deren Schutzschichten (metallisch, keramisch) oft in kurzen Zeiträumen und lokal mit äußerst unterschiedlicher Dynamik (Abzehrrate). Dadurch kann es unerwartet und plötzlich zu Rohrleckagen kommen. Die Folge sind ungeplanter Stillstand und meist hoher Reparaturaufwand.
01 Revisionsbegleitende Maßnahmen
– mit Kesselbegehungen im verschmutzten und gereinigten Zustand frühzeitig Schäden vorbeugen
Eine vorausschauende Instandhaltung kann vor ungeplanten Stillständen bewahren, sofern sie während der Revisionen fachkundige Begehungen einschließt. Wir übernehmen solche Maßnahmen sowohl im verschmutzten als auch im gereinigten Zustand des Kessels. Dabei untersuchen wir den gesamten Rauchgasweg mit allen zugänglichen Bauteilen. Wir erfassen die räumliche und zeitliche Dynamik von Korrosion und Erosion und erhalten letztendlich ein detailliertes, aussagekräftiges Zustandsbild. Dabei führt nach unseren Erfahrungen eine schrittweise Begleitung zu einem bestmöglichen Ergebnis.
Schritt 1: Begehung im verschmutzten Zustand
Schritt 2: Begehung im sauberen Zustand
Schritt 3: Qualitätsbegleitende Maßnahmen im Revisionsablauf
Im verschmutzten Zustand liefern uns lokale Anomalien in den Eigenschaften der Verschmutzung (Form, Dicke, Farbe, Härte, Schmelzfluss etc.) wichtige Hinweise auf dort auftretende besondere Bedingungen. Daraus können wir potentielle Risikobereiche des Kessels in Bezug auf Korrosion und Erosion ableiten.
Im gereinigten Zustand betrachten wir alle relevanten Wärmetauscherflächen und besonders die zuvor erkannten Risikobereiche. Diese Beurteilung erfolgt mit dem Auge unserer erfahrenen Spezialisten und wird durch Ableuchten der Wärmetauscherflächen mit streifendem Licht unterstützt. Auf diese Weise können wir in den zugänglichen Bereichen – von stichprobenartig bis zu 100 Prozent eines Bauteils – die am stärksten von Korrosion und Erosion betroffenen Stellen identifizieren. Wir markieren diese Stellen und bewerten sie dann, indem wir die Restwanddicken bzw. Schutzschichtdicken messen.
Parallel zu lieferantenseitigen Reparaturen und Applikation bieten wir qualitätsbegleitende Maßnahmen an. Hierbei leisten wir bei der Applikation von Werkstoffen einen neutralen, zusätzlichen Impuls, dass Qualitätsanforderungen sicher erfüllt werden. Der wesentliche Aspekt dabei ist, dass wir die spezifischen Qualitätsanforderungen aus der Einschätzung der späteren betrieblichen Belastungsprofile ableiten können und damit das Erreichen von maßgeschneiderten Leistungsmerkmalen der Werkstoffe unterstützen.
Eine entsprechende CheMin-Datenbank archiviert und dokumentiert alle erzeugten Daten. So werden für den Betreiber im Verlauf mehrerer Revisionen die Bauteilentwicklung und deren Restnutzungsdauer klar erkennbar und zeitlich optimierte Wartungsmaßnahmen planbar.
Dieses Vorgehen ist sowohl auf drucktragende Werkstoffe anwendbar sowie auch auf die darauf applizierten Schutzschichten (Cladding, thermische Spritzschicht etc.).
Unsere Erfahrung belegt klar, dass die zunächst optische Betrachtung und das darauf begründete Markieren besonders auffälliger Bereiche gegenüber den rasterförmigen Messungen der Restwanddicke / Schutzschichtdicke deutlich überlegen ist. Eine Rastermessung erfasst keine lokalen Anomalien. Ein Beispiel: Bei einer solchen Messung am Rohrscheitel wird eine mögliche Abzehrung an der Rohrflanke nicht erfasst, so dass der Zustand des Rohres vermutlich falsch beurteilt wird.
02 Betriebsbegleitende Maßnahmen
– Tests, Befundungen und sensorische Daten erschließen Prozessmerkmale und ermöglichen, die Eignung der Werkstoffe und die Performance der gesamten Anlage zu optimieren
Je komplexer und variabler die chemischen Nebenwirkungen der Brennstoffe sind, desto höher sind die Anforderungen an die Eigenschaften und die Qualität der eingesetzten Werkstoffe und deren Applikation. Dies gilt insbesondere bei den „schwierigen Brennstoffen“ Abfall, EBS, Biomasse und Klärschlamm, aber auch bei fossilen Brennstoffen und bei der Mitverbrennung.
Häufig ist es so, dass die einzelnen Gewerke beim Bau einer solchen Verbrennungsanlage den späteren Nutzungsanspruch nicht ausreichend einschätzen können. Besonders aggressiver Brennstoff, eine sehr hohe Energieeffizienz der Anlage oder lange Reisezeiten bzw. der Zwang zu hoher Verfügbarkeit können solche hohen, schwer einschätzbaren Ansprüche auslösen.
Unsere betriebsbegleitenden Maßnahmen nutzen den realen Prozess, um:
- Werkstoffeigenschaften zu untersuchen
- Werkstoffentwicklung zu unterstützen
- Prozessmerkmale und ‑ursachen für Korrosion und Verschmutzung zu detektieren
- Prozesseigenschaften zu ermitteln und zu optimieren
- Auswirkungen von gezielten Veränderungen (Tests) zu erkennen und zu bewerten
Gerne kooperieren wir auf vertraulicher Grundlage mit den Herstellern, Verarbeitern und Anwendern der Werkstoffe. Wir stellen unsere Befunde und Anhaltspunkte für die Weiterentwicklung von Materialien – nicht nur Kraftwerkswerkstoffe – und deren Herstellungsprozessen zur Verfügung
Als Entwicklungspartner für verbesserte Werkstoffe und Applikationen nutzen wir bevorzugt den Weg der praxisnahen Erprobung. Das heißt, wir entwickeln je nach Problem und Aufgabenstellung spezifizierte Werkstoffsonden, die wir dann unter realen und zielgerichteten Milieubedingungen einsetzen (siehe CheMin-Sonden und ‑Sensoren). Dadurch können wir die Leistungsmerkmale von Werkstoffen wesentlich klarer aufzeigen, als dies durch Labortests möglich wäre. Unsere Erfahrung zeigt, dass dieses Vorgehen dem Einsatz genormter Tests und entsprechender Prüfstände in vielen Fällen überlegen ist.